|
|
Mail
and Frequently Asked Questions about Construction Techniques
These are questions I have received from visitors
regarding construction and building techniques and related issues. Other
Mail and FAQ Pages
Also see
|
|
|
On
shear webs, I think you may want to look at ANC 18. Here is the part that discusses shear webs and spars:
Wood Beams in Aircraft.
In my current designs I use 1/64 ply for shear webs The samples
I have weighed are about the same as contest 1/16 balsa so there is little or no weight penalty. I use box spars
with the shear web on front and back faces and vertical balsa siffeners at rib locations.
After looking at this document and discussing it with other model
builders, some with engineering backgrounds, I think the best grain orientation for shear webbing is at 45 degrees.
Since the 1/64 ply has three laminations the front and rear webs probably should have their 2 ply directions at 90
degrees to each other.
I understand the the very strongest webs would be at 45 degrees to the spars in
both directions — in other words plywood but at 45
degrees instead of vertical. In my case, I would laminate balsa to make them lighter just because I’m OCD like
that.
But, I’m not that motivated either so unless it’s very critical (thin wing when
absolute highest strength is necessary) I’m sticking with the vertical webs. I added the link you provided to the
shear webs page. Thanks!
Top
|
|
|
Which do you think would be
better, the
Adjusto wing jig that you mention on your site or the
magnetic building system?
For straight wings (no taper) I
prefer to build on the magnetic board. For tapered wings I prefer the wing
jig.
That’s how it goes overall.
No tool does everything so having a variety gives you a better chance to have
the “just right” tool in any given circumstance.
Top
|
|
|
Please can you help me out
with these solder clevises? I am at a loss. I have tried but just
end up with burnt fingers and a black and blobby mess. And the funniest
thing about it all is the clevis fell off the pushrod when I was done, landed on
my foot and burnt a hole in my new Nike's. I am thinking about throwing
the solder clevises away and using Z bends instead.
I feel your pain — or at least I used to.
Until somebody showed me how to solder I had the same problems — cooked joints,
solder that didn’t flow, burns on various areas of my body, and people around me
learned all kinds of colorful new words they’d never heard before.
The first thing you need to do is make
sure what you want to solder is clean. Put some alcohol in a small
container and soak the clevis or use a pipe cleaner with alcohol on it to clean
the inside of the clevis.
Clean the wire with steel wool or very
fine sandpaper.
When everything is clean and dry, apply
non-corroding paste flux (available from any hardware store) to the wire where
the clevis will go. You can also apply some inside the clevis with a
toothpick.
Slide the clevis on the rod where you
want it. There is a seam in the clevis shank. Arrange it so that the
seam is up. That’s where you’re going to apply the solder.
Make sure the tip of your soldering iron
is clean and tinned. If it’s black and cruddy you’ll never get it to work.
While the iron is cool, clean the tip with steel wool. After it’s heated you can
dip it in the flux and then melt a little solder on it. Most people wipe
the iron on a wet sponge, but that only works if the tip was tinned properly to
begin with. Being very careful shake excess solder off the tip.
The tip should be bright and shiny.
Apply the tip to the underside of the
clevis shank. Apply solder to the seam on the opposite side (top). When
the clevis is heated enough you’ll see solder melt and flow into the clevis.
Apply a little more solder to the end of the clevis to make a small fillet
between it and the rod.
Remove the soldering iron and let the
solder cool. Do not move the clevis or rod while the solder is molten or
you’ll get what’s called a “cold” solder joint. A cold joint is dull
looking and extremely weak.
Top
|
|
|
I was told that I could wet a
wing skin with a combination of ammonia and water and it would make the skin
flexible enough to form it around leading edges and not crack or break.
Have you ever heard of or done anything like this? If so could direct me
on how to do this and all other details.
I have done that, but it’s a last resort.
Ammonia does very bad things to wood. For one thing it turns it to pulp
while it’s wet and can create undulations where the tape held it while it dried.
These waves in the wood will be present after the wood dries and nothing will
make them go away. It doesn't always happen, but you have to be careful
how much pressure you use and how well it's distributed.
When water and especially water and
ammonia is used to bend wood it makes the wood somehow different. I can’t
say exactly how, but it does not behave the same. The grain also opens up
more than if you hadn’t wet it first.
If you must wet the wood, try warm water
first. Don’t use ammonia unless you absolutely have to. Normally
leading edge sheeting will bend into place without any wetting necessary.
If the wood is so hard that it needs to be wetted then the wood should probably
be replaced with more appropriate sheet.
Top
|
|
|
I am looking for an easy way
to make a full-chord wing fairing at the fuselage joint on an airplane having a
removable wing. This is for scale effect. A removable belly pan is
also involved so there needs to be a break at the leading edge.
Do you have a system for
adding this feature on my small 1/12th scale P-47? I can envision starting with
the waxed paper over the wings and using epoxy/micro balloons and shaping it
while it's in a putty stage of cure.
There are several ways to go
about it. The lightest way is the most difficult. Cut triangle pieces of
sheet and glue them to the fuselage. Sheet over the triangles with thin
balsa. Usually the triangles are concave on the top.
The heaviest way is to use a
putty — most commonly
epoxy and
micro-balloons. It is done just as you have said but I would use
plastic food wrap or the clear backing from iron-on covering rather than waxed
paper.
One way I’ve done this is to put
plastic on both the wing and the fuselage. That allows me to remove the
fillet after it’s cured and shape it separately. I add chopped fiberglass
to the epoxy/micro-balloon mix to strengthen it somewhat.
Another way is to cut a thicker
sheet of balsa to match the airfoil and glue it to the fuselage. Carve to
shape.
Choose your poison.
Top
|
|
|
I have read your article
How To Make Tapered Wing Ribs. I have read other articles dealing with
stacking balsa between templates and Drilling and bolting them together.
What no one has said was how the stack was drilled successfully without
destroying the balsa. Can you explain to me how you drill the holes in the
ribs you make?
I use several methods for
drilling balsa depending on what type of balsa I’m dealing with.
For very thin and soft balsa I
used sharpened brass tubing.
For harder balsa of any
thickness I use brad point drill bits.
For thicker soft balsa I cut
teeth in a brass tube such that the teeth angle away from the direction that the
tube rotates.
The ribs in the article are soft
contest balsa except for the tip and root ribs. I stacked up about 5
blanks and used my drill press with a brad point bit. It did chew up the balsa
somewhat. It didn’t matter in that I only clamp the ribs together one time
so as long as the bolt could pass through and be tightened to prevent the rib
blanks from shifting, it didn’t matter if the holes weren’t perfect.
Top |
|
|
What procedure do you use in
sanding the wing parts in preparation for the covering without breaking any of
the ribs and spars?
I use a long T-Bar sander and
sand front to back. I move frequently between groups of ribs (the ones
covered by the T-bar) so that I don’t sand too long in one spot. I also
overlap by moving over a set number of ribs each time — three, for example.
The wing needs to be braced so
you can hold the sander with both hands. Take your time and work slowly. If you
start scrubbing you’ll screw something up that is hard to fix.
It is possible to sand a spar
down to match the ribs without hitting the ribs, but again, it means bracing the
wing, using both hands and going slowly. Sight from the end so that you can see
if the sander is rocking and hitting ribs. When the spar is way oversize, put
masking tape on the ribs to protect them. When you start hitting the tape,
remove the tape and from then on go slow, be careful.
Top |
|
|
I want to scrap-build a
1975 Sun Ray from RCM plans. The bottom wing is a gull wing. The
instructions tell you to construct the gull wing spar from a single continuous
piece of birch plywood (38" span).
This seems heavy (and silly) to me. I was thinking of
constructing a balsa spar and laminating it with fiberglass. Then, I was
toying with the idea of fully sheeting the wing and fiberglassing that too.
I thought it would be best to glass it in sections, feathering and overlapping
layers of cloth where the gull wing bends. Will that be strong enough?
Before going into the answer
here's a warning. RC Modeler Plans (RCM) are still being sold but they
are not delivering. Why the State Attorney General hasn't stepped in I
don't know. But DO NOT attempt to purchase any RCM plans. You'll
just lose your money. Hopefully when you figure it out your credit card
company will get your money back. But whoever is behind it is scamming
people. I hope it's not anyone who was actually associated with the
magazine because it was a great magazine for the many, many years it was
published.
|
Having never a built a model such as this, I can’t say from
experience how you could lighten the structure while maintaining necessary
integrity. I would follow the plan for the most part, but I would use light
woods as usual and remove excess “beefing” which is almost certainly present
given the year the model design was published.
That being said, I don’t think you’ll save any weight by
building a fiberglass spar. The effort would be considerably more than cutting
out a
plywood spar and in the end it may end up heavier and might also be weaker.
I would probably extend the plywood spar slightly into the out
panel, but not the full span. The landing gear is located at the outer gull so
the spar must be strong enough to prevent the wing from breaking during normal
landings.
If money is no object and you have a way to safely fabricate
it, a carbon fiber plate spar should save weight and add considerable strength.
I have not cut CF other than to trim little bits here and there. I’ve heard
that scroll saw blades pretty much bounce off the stuff. You could probably cut
it with a scroll saw but it may take hours. A band saw may work better.
If you choose to go with the plywood then you may be able to
make some cut-outs in it as long as you keep them away from the gull angles.
As far as
glassing goes, I agree with your approach. Trying to glass the wing in one
piece will probably be frustrating and may leave areas where the glass didn’t
lay down properly. But lightweight fiberglass is not going to strengthen the
gulls enough to do away with a spar strong enough to handle the landing gear
loads.
If you can conceive of building more than one of this model
then you may want to try some things and see how they work out. If your
modifications hold up then you may want to go even further on the next one.
Top |
|
|
I was looking through your website and I thought I found it
but I can't seem to find it again. If I was mistaken I would really like
your method of building tapered wings or please help me to find the article.
The method I use to cut the ribs is about halfway down on this
page:
Model-Building Tips - General Construction
It’s an old concept (not mine) that I have used with excellent
success.
Top |
|
|
I have (once again) gotten myself interested in building
model airplanes. I used to stick to White wings paper airplanes (and design
my own) because they are cheaper to design, build, and buy. However, I've
finally decided to move on up in the world and build balsa models.
I've got an electric engine that used to belong to a plane
my dad bought for me one Christmas not too long ago, but I dismantled the
airplane (to see how it was built) not long after I got it, and most of the
pieces were lost in the shuffle.
I've decided to design one and build it (I'm actually going
to college for Aerospace Engineering, so this should be a lot of fun).
How do I mount an unsheeted wing with a small dihedral?
I'm thinking about making the dihedral 5 degrees and the wing will be mounted to
the top of the fuselage. What kinds of coverings are available that don't
iron on yet are light and strong? Thanks for your time (and for your
website).
A well built model of any type is a good model and one to be
proud of. I have some White Wings and have enjoyed them.
Does the wing have to be unsheeted? If you can at least sheet
the center you’ll have an easier time of it.
If you don’t use any sheeting at all you’ll need a block glued
between the ribs and against the trailing edge of the wing. Drill through the
block for a pair of bolts that will thread into hardwood blocks or a plywood
plate in the fuselage.
You’ll also have to glue a couple dowels through the leading
edge back into a piece of wood glued between the spars. Drill holes in the
former in the fuselage at the front of the wing to match.
I’m assuming this won’t be a very large plane and you’ll be
able to get away with that. If the plane is subjected to much stress then there
is the possibility the system won’t hold and you can imagine the result of a
wing parting company with the fuselage in flight.
As far as
coverings go, the ones that don’t iron on are applied with dope. I suggest
you stick to plastic and concentrate on learning about design and construction.
Later when you build better models start looking at better finishes. I only
paint my best models because it’s expensive and tons of work.
Painted finishes include doped on
silk, silkspan, tissue, Koverall, Stits fabric and some others. Another finish is
fiberglass that is then painted with whatever you like. But fiberglass can
be applied only to solid wood. You can’t apply it over open construction.
Top |
|
|
I have an ABS plastic cowling for a 1/4 scale J3 cub and I
would like to modify the cowling fit by cutting it in half top and bottom.
My question involves cutting and rigging the cowling so it
will not be destroyed by vibration. This arrangement will make it easier
to get the cowling on and will allow the opening form the side mounted engine to
be a minimum size.
I would fiberglass the inside of the cowling before cutting it
to help prevent vibration from cracking it. I would make a 1/32” plywood lip to
glue to one half of the cowling and use #0 or #1 wood screws to attach the
second half to the first half.
When you mount the cowl to the fuselage you must support it as
perfectly as possible with no distortion. If the fuselage wedges into the cowl
then sand some of the fuselage away so that the cowl fits as smoothly as
possible without the fuselage trying to expand the cowl. If the cowl is bigger
than the fuselage then be sure the cowl mounting blocks are right against the
inside of the cowl so that when you tighten the mounting screws the cowl doesn’t
bend in.
Use plenty of screws and don’t over tighten them. Just snug
them. It’s best if you use hardwood blocks and wood screws. Harden the threads
in the blocks with thin CA.
Top |
|
|
I have a construction question. I'm trying to figure
out a way to make an access panel. It's to get to the motor compartment.
The plan calls for dowels and rubber bands but I think that looks ugly. I
would use magnets but I don't want the field to interfere with the motor.
Any ideas?
I've always wanted to build one of those. It's
definitely an attention getter! I agree that the rubber band method isn't
too attractive.
I would simply glue a couple small triangles of 1/16" plywood
into the corner in front of the former at the leading edge of the wing and above
the dowel.
Use a couple #0 or #1 wood screws to hold the hatch down.
You can either inset a small piece of plywood into the balsa hatch or just
harden the holes in the balsa with thin CA and not crank the screws down too
tight.
Top |
|
|
I am inquiring about what is the correct way to install CA
hinges. The plane I am building has large control surfaces and I am
concerned about failure.
I don’t use CA hinges because I think they are the worst
excuse ever for
hinges. I suggest you use pinned flat hinges, such as Dubro or Robart Hinge
Points. I can’t tell you the proper way to install CA hinges having never used
them.
I have written a tutorial regarding
Robart Hinge Points if you’re interested.
Top |
|
|
I am having difficulty
building open structure wings that do not warp (more like bows) when the leading
edge and trailing edge sheeting is applied.
I use magnets to build with
and heavy weights to keep things where they should be. Before the wing
sheeting is applied, the wing is nice and straight.
Once the Sheeting has been
applied the wing becomes extremely rigid and the warp is permanent. The
leading edge on the wing I am building does not have a false leading edge but is
a 1/2" square stick inserted in the ribs so it looks like a diamond shape.
If you have any suggestions I sure would appreciate them.
It’s difficult for me to tell
you exactly what the problem is when I can’t see the actual pieces used in the
wings you are building.
More often than not balsa sticks
are warped. I cut my own sticks and they almost always bow or warp when
they are cut from a sheet that had a straight edge before I stripped the sticks.
Narrow sheets can do the same
thing. For example, a 1” wide balsa trailing edge sheet can curve along
it’s length. Even with these warped parts I don’t have problems building a
straight wing. It has more to do with technique than anything else.
Here are some things you can do:
-
Be sure to acclimatize your wood. Before you
start to build, the kit should be in your shop for at least a week. It’s best
to leave the box open during this time.
-
Use a straight edge to align spars, trailing
edge sheet, etc. on the building board. Don’t trust the lines drawn on
the plans.
-
Use slow-drying glue. It allows the parts
to be put into the correct position (straight) before the glue dries.
-
Install warped parts so they oppose each other.
For example, if there is an upper and lower main
spar and they are both bowed at one end, set up the spars so that they bow
"in" with the bow at the same end of the wing. In other words, the
concave side of the spar part should be outward.
If the part is very hard and requires a bit of
effort to make it straighten out then it should be replaced. Use a bowed
piece only when it takes very little effort to make it straight.
-
Install upper and lower sheeting the same way.
-
Single parts that don’t have a match, such as a
leading edge, should be installed so that the bow is forward or backward.
I like to install it so the concave side is forward.
The spars and trailing edge will prevent the
leading edge from curving the wing front to back. If you install the
leading edge with the bow up or down then it can cause the wing to bow in the
same direction which I think is what happened to your wing.
-
You say you use lots of weight and magnets to
hold things in place.
Do not place magnets or weight over unsupported
sheeting. For example, if you put magnets on the upper trailing edge
sheeting, place them in a location where there is a rib under the sheeting.
Otherwise the magnets will bow the sheeting down while it dries. When
the magnet is removed, the stress will be relieved and can cause problems.
-
Be patient! Allow glue to dry thoroughly
before removing the weight or magnets. It is always said to wait 24 hours.
That is absolutely correct. 24 hours isn’t overnight – it’s 24 hours.
It’s not just the glue drying, but the wood taking a “set.” The longer
you can leave the wing on the board, the better. If it's not in the way
and you have other things to work on, just leave it.
-
A thick part that is warped should be replaced.
For example, tapered trailing edge stock probably won’t stay straight even if
it is bent so that it glues on straight. Better is to use a piece of
straight stock to begin with or carve and sand your own tapered stock. I
usually glue a sheet in place and sand it to shape after it is dry.
Top |
|
|
How do you transfer your pattern from the plan to your wood,
especially if you have many identical pieces to cut?
There are a lot of ways to transfer the pattern:
-
Put the drawing over the wood and use
a pin to punch holes through the outline to create an outline on the wood.
-
Same as above, but then rub colored
chalk through the holes onto the wood.
-
Turn the plan upside down over the
wood and use a hot iron to transfer the drawing onto the wood.
-
Trace the pattern on to clear plastic
such as overhead projector transparency material. Cut out the patterns
and then trace around them on to the wood.
-
Make a copy of the plan and then use
spray glue to put a light coat on the pattern only. Allow it to dry to the
point where it is not really sticky and then rub the pattern down on the
wood. The pattern can be peeled off after the part is cut out. This is the
method I always use.
If I have to cut a lot of identical pieces and it’s a short
stack then I stack up the wood and use my scroll saw.
If it’s a tall stack, such as ribs, I make a hard pattern and
cut each piece individually using a hobby knife around the pattern.
If the part is a rectangle, such as
shear webs in a constant
chord wing then I use my
table saw. If I didn’t have a table saw, then I would
cut around a pattern to make them.
Top
|
|
|
I have decided that my next
project will be a 40-sized sport-scale PT-17 Stearman. Problem is, I have
not been able to find any acceptable plans for this. Nick Ziroli Jr. has
some lovely scale plans for giant size, but I don't want to build something that
big (yet).
On the other hand, I found a
"stand-off scale" plan for the PT-17 drawn by Nick Ziroli Sr. back in 1973 from
Carstens. There are, however, a few things I need to tweak and I would
appreciate your thoughts.
Ziroli's fuselage deviates
further from true scale than I am prepared to accept. He put the engine
out front and exposed, which is fine in a trainer or a fun-flyer but I want a
plane that looks like a Stearman while in the air. So, I need to redo the
fuselage to match the true outline and put the engine/muffler inside. This
will entail shortening the moment forward of the CG by between 1/2 and 3/4 inch
(on a total length of 40"), but not really shortening the length aft.
Obviously, this then requires that the aft section be built much lighter than
Ziroli's original to avoid having to load up on lead weights in the nose.
Question 1) Ziroli
called for a solid slab stab and fin/rudder, using 1/4" balsa. Seems to me
that this is too thick and is likely to warp as well. In your
Hammerhead design you used 1/8" sheet with 1/8" ribs sanded to shape, for a
total thickness of 3/8 or so.
Since your plane was bigger
and more powerful than my planned 51" span and 0.46 engined Stearman, I was
wondering if you thought that 1/16" or 3/32" sheet with 3/32" ribs (and with
holes drilled in the sheet) would be strong enough - or should I avoid a sheet
core entirely and build a completely open empennage framework?
Question 2) Ziroli's
fuselage design calls for a solid 1/8" balsa box with doublers at the nose and
formers throughout. I am wondering if I could go for 1/8" lite ply from
the wing trailing edge forward, cut out in the middle for lightening and doubled
at the wing root with either ply or balsa. The aft section would be open
frame with Warren trussing (similar to your Hammerhead) - I was thinking 1/4" x
1/4" balsa for this.
The outer shape would retain
Ziroli's 3/8" x 1/8" stringers sanded to match the cross section. Would
this be lighter than the original all-sheet box? Would this be strong
enough - or alternatively is 1/4"square framing excessive on this size model?
The wings in the original are
fine as they are, although I will probably want to cut holes in the ribs to
lighten them a bit. Any thoughts you have on these issues will be very
helpful. Cheers!
Another place to check for plans
is
Cleveland
Plans.
Back in the day almost all
models were over-built. The philosophy was to build models to withstand a
crash. It took a long time for us to realize that isn't the way to do it.
A better philosophy is to build
to fly and expect the plane to be totaled in a crash. At first that may
seem foolish, but there are a lot of advantages to building this way.
First, our radios are much more
reliable than they used to be. Radio failure is not the cause of most
crashes.
Second, a plane that flies well
is less likely to crash. Why build a plane that always flies like a dog
just so that it might survive an unplanned impact with the ground? Better
to have one that flies well for its lifetime however long that may be.
Lastly, a thing a lot of guys
don't think about is that a lighter aircraft not only flies better, but the
lower amount of mass amounts to less inertia in the event the plane does crash.
What that means is that it has a better chance of surviving impacts.
Great
Gonzo is an excellent example of this. I can't count the number of
times I attempted zero ground speed landings with her only to have her drop out
of the sky from 15 feet straight on her nose. Never once was there any
damage incurred other than a few broken props. It was so light that it
just bounced off the ground.
FYI, the tail on Hammerhead is
about 3/4" thick. But I would not build the tail for your plane as I did
for Hammerhead. I think your second idea is better. Use ribs only,
but skip the balsa core.
What I would do is cut
rectangular rib blanks and use one basswood spar in the middle of the ribs so
that it won't show under the covering. A single, full-span 1/8" x 1/4"
spar should be fine.
Use a firm balsa leading edge.
Once the whole thing is glued together, sand the surface to an airfoil shape.
It's not as hard as it seems at first. Just take care to keep it
symmetrical from one side to the other.
I would use 1/16" ribs for the
tail surface. They will look closer to scale and save you a bit of weight.
Take a look at the
photo page
for Rustik to see how the fin/rudder assembly was built. That's more
or less what you want to do, but add the spar and skip the sheeting. As
long as you don't do high-speed dives, it will be fine.
Forget about lite ply in the
fuselage and everywhere else for that matter. Lite ply doesn't carry its
own weight and is generally a poor choice for model aircraft construction.
Use contest balsa for everything
but spars and leading edges. You can probably make the fuselage sides from
3/32" balsa with a 1/64" doubler if there is a structure built around the
basic box. Otherwise I would stick to 1/8" sides and still use a 1/64"
doubler.
1/4" square longerons are the
way to go. 3/16" square probably won't be stiff enough and the weight
savings will be negligible. I built Great Gonzo using 3/16" longerons but
I wouldn't trust them to build a fuselage that is stiff enough for a .40 size
model.
What you can do is make the
stringers from thinner stock — maybe 1/16" x 3/8". They'll be a little
harder to work with because they'll try to flip on their side when you bend them
to match the curve of the fuselage.
Start by gluing them at the
forward most position and use thin CA to glue them in place working your way
back. Draw lines on the fuselage sides to keep the stringers straight.
Wavy stringers look bad under covering.
I also suggest using pull-pull
controls to the tail surfaces. That will save you at least a few ounces of
weight behind the CG.
Another idea is to finish the
tail surfaces with tissue and dope. It will work well, although you'll have
to handle the model carefully so that you don't punch holes through the tissue
covering. Tissue and dope will be lighter than Monokote or Coverite.
One way to get some weight up
front is to build one of the William's Brothers scale engine kits. They're
fairly heavy which is good and bad. Good because it helps with the
balance, but bad because all weight is bad.
A way to save a lot of weight on
formers and increase the strength is to make
balsa plywood.
You can cut the formers to have
about a 1/4" outline and they'll still be strong enough and stiff enough to work
well. Use your judgment on how much to cut out of a former. If in
doubt, make the cut-out small at first. You can always cut out more if you
think it will be ok.
If you choose to paint the
model, spray light coats and sand between every coat. That will keep the
paint thin and light. Thin coats of paint are much less likely to peel or
chip and weighs less than standard weight iron-on films (standard weight being
Monokote, Oracover, etc.).
If the model is truly a .40
size, then I recommend using the O.S. .52 4-Stroke. It's an awesome engine
and a perfect match for a Golden Era biplane.Top
|
|
|
The aileron in the kit that I
am building is bowed. There does not seem to be any twist to it. My
question is how to get the bow out.
The only method I know of to
*attempt* to remove a bow is to bend the wood past what would be straight and
hope for the best.
The reason you go past straight
is that the wood will spring back slightly. Before you bend the wood you
can steam it, moisten it with water using a paper towel (don't soak the wood) or
use heat.
If the aileron stock wasn't that
great to begin with, then a bow might just be the "last straw" and prompt me to
replace the aileron instead of mess around with it.
Because I build with magnets, I
can set up a few fixtures to hold the piece so that it is sitting on the leading
edge and adjust the fixtures so that the piece is bent as indicated above.
Another way is to place the
aileron on a dowel that is padded with a rag or paper towels and then place
weights on the ends.
No matter what you do, you're
guessing as to how much to bend it. Normally about 100% is a good place to
start. In other words, if the ends are 1/4" higher than the center, then
bend the ends 1/4" past center in the other direction.
Once you get the piece jigged how you like it, let it stay
there about 24 hours so that it will take a set. You might need to repeat
this more than once to get the bow completely removed. Whether it's worth
the trouble rather than replacing the part is your decision.
Top
|
|
|
I really liked reading your site on
wing building. I'm going to re-build one I crashed the other WINDY
day. Building is 1/2 the fun to me. What type of wood is
used in a trainer wing spar? The broken one seems to have a reddish color
to it. Also where's a good place to order balsa wood from?
As far as your wing spar goes, there is no set material to
make them from. Normally they are made from balsa, but sometimes they are spruce
or basswood. It all depends on what the designer was thinking when he was
at his drafting table.
Repairing spars is a tricky proposition. If you haven't
done it already, then I strongly suggest that you seek out a better builder in
your area to give you first hand guidance. Spars are critical structural
members and if they aren't repaired properly you can expect catastrophic failure
of the wing.
What you'll need to do is put the broken pieces back in place
as well as possible. Then splice in pieces to fill the gaps so the spar is
one piece again with no missing areas.
That will not be strong enough on its own. You should
then take some 1/32" or 1/16" plywood and splice a piece on the front and the
back that extends about 5" on both sides of the break (10" in all).
Toward the end you should taper the plywood to a point.
Otherwise what you will be creating is called a "stress point" where the wing
will naturally want to break again. That point will be where the plywood
ends. The taper spreads the stress out over a larger area so the wing can
bend instead of break.
It is easier to draw than to explain. Again, seek a good
builder to help you out.
Sources of balsa are listed at the end of the
Balsa Wood page.
Top
|
|
|
I will be starting to build with
magnets mostly due to your site and all the positives that your site
provides on building this way. The one question I have is when building
tail feathers. How do you hold parts down so they don't bow up?
The technique I use depends on how the surfaces are built.
For built-up stick tail surfaces I put a magnet (without plates) on each side of the
sticks. The magnets are set up such that they are attracted to each other (with
the stick in between) which puts pressure on the sticks. Then I just push the
sticks down on the board and they tend to stay there. Weight can be added
if necessary, but if the part is bowed to begin with then I normally don't use
it.
For solid surfaces that have edge-joined parts or
cross-grain tips, I put a
straight edge with a magnetic strip attached to the bottom on the board. Then I
push a straight edge of the largest piece of the surface against the magnetic straightedge.
That locks in one side.
I use magnets to push the edge-joined parts against the larger
part. I normally put more magnets or other weight on top of the structure to
hold it down while it dries. I normally use
Ambroid
glue to edge-join because it
dries fast and sands well.
Tail surfaces tend to bow after they are built. Long, flat
surfaces just don’t like to stay flat. For that reason, I almost always build
them thicker than what is called for. For example, if the tail is to be 3/16”
thick, then I build it from 1/4” wood. Then I can sand it flat after it is
complete. A bow isn’t a big deal, but it bothers me enough to do the extra work
to make sure my models don’t end up with them.
Warps are a different story and are more than an annoyance.
My structures don’t warp, but they do bow sometimes and I take care of
them as above. Warps are normally due to
using warped wood to begin with or from putting too much pressure on the
structure when gluing it together. Ensuring that parts mate well before
gluing them allows a modest amount of clamping pressure to be used without
building in unwanted stresses.Top
|
|
|
While reading thru your site I found mention of shaping the
leading edge and was wondering if you could elaborate more on this. I am
putting together my first kit and need to shape the leading edge. I have
planed down the edge and now need to provide the round shape. The issue I
have is this wing tapers down from one end to the other so the leading edge will
differ in size. How do you sand down the edge to the rounded leading edge?
What you’re asking me to describe is really a technique that
has become second nature to me through sanding a heck of a lot of leading edges.
I’ll try to explain it, but what you need to know is that for it to become
automatic for you, you’re going to have to build a lot of planes.
That doesn’t mean you can’t get every leading edge you ever
shape right, but you’ll have to stop more often, check that you’re on track and
make a lot of corrections.
I work on the top and bottom of the leading edge separately
until it’s ready for finish-sanding.
First, I plane the top so that it is tangent to the ribs for
the full span, but leave about 1/32” or so left to sand. When I say,
‘tangent’ what I mean is parallel to tangent. Tangent would actually be
flush with the front of the rib, but I don’t plane down that far. It is
too easy to remove too much wood.
If the leading edge tapers as you describe, then I start
towards the tip and with each stroke of the plane I move more towards the root
and plane all the way to the tip. This technique removes more wood from
the tip than from the root. I adjust as necessary. If I’m removing
too much wood at the tip, then I might stop short of the tip for a few strokes
until it evens out.
Once the top is tangent, I use the plane to start rounding
over from the back edge of the leading edge to the front. Again, I work
slowly and check my work frequently. When I’ve gotten as close as I feel
comfortable getting with the plane, I flip the wing over and repeat the same
steps for the bottom of the leading edge.
Now it’s time to switch to sandpaper. I use a long T-Bar
sander with 150 grit paper to rough in the shape. Again, I work on the top
and bottom separately. I sand spanwise while rounding the block over the
front of the leading edge. I use this block until the shape is exactly
what I want and the back of the leading edge is flush with the ribs.
Now I switch to finer sandpapers to finish sand. By the
way, I shape the everything before I even think about finish sanding. If
you finish sand one part and then shape another, you still have to make the two
parts mate. What is likely to happen is that there won’t be enough
material in the part you finish sanded. Better to not do any more sanding than
necessary until everything can be sanded at the same time.
In some cases, it’s harder to sand a part after other parts
are glued around it. In this case, it is often best to sand the part while
you can. Use your judgment and think ahead.
One thing you’ll need to learn how to do is vary the amount of
pressure you put on a sanding block to deliberately sand in or remove a taper.
That is a “feel” thing and there’s no real way to tell you. You just have to do
it a few times and see what happens. For example, you can shape a tapered
leading edge from start to finish with nothing but a sanding block. Put
more pressure on the end that has the most taper until the angle is right. Then
sand evenly from then on.
Top
|
|
|
I just read your tutorial on
rib-making, and read that you cut out the "central" part of all your ribs
for weight reasons. Do you think I can do the same on a Giant Scale (77")
Ziroli Stearman PT17? Or does the cutout reduce the strength of the rib by
too much?
Yes, I believe the ribs will be strong enough even with the
interior portions removed. You will have to use your judgment though, as I
haven’t built this aircraft.
I would not modify ribs that are load-carrying. For example,
ribs near the center section, interplane struts or cabane struts should probably
be left intact except for possibly holes to pass servo leads.
Other than that, I wouldn’t worry too much. Ribs are more for
providing shape than for strength.
Top
|
|
|
I read with interest your article on
plywood landing gear laminated with
f-glass cloth. I need to build a set for a scratch built plane and
wondered if you have any further suggestions. I was going to use 1/32 ply
but it may too difficult to bend.
Seems like your gear originally might
have been too flexible. How can we stiffen it up without getting into
carbon fiber? Any further suggestions will be appreciated and keep up the
good work of passing on your projects.
Eli Whitney tried 61 times before
his cotton picker worked!!
I used 1/64” ply simply because it was much easier to bend
without fear of it cracking in the bends. I ended up adding another lamination
of 6 oz glass cloth and then a 6th lamination of ply to the original gear. It
is very stiff now and I think it’s going to work well. I’ve played around with
it a bit – bending, twisting, etc. and it seems good.
The plane is almost finished, so I’ll be able to see what
happens in a real-world environment. Until then, all I can say is that I trust
it or I wouldn’t use it, but the proof will be seeing it hold up after a few
hard landings.
As of now,
Rustik
has several flights and the gear has performed flawlessly. I store the
model standing on the spinner to prevent the gear from warping due to the weight
of the model.
Top
|
|
|
Is it possible to build a Gee Bee Z into a biplane?
There is one on my flight simulator and it looks awesome.
I don’t see any reason it
could not be made into a biplane. Gee Bees are known to be squirrelly aircraft
and making it a bipe might make it even more so. I would narrow the wing chord
a little if I were to do this. Most Gee Bee models have longer
moments than
what is scale to make them easier to fly.
This would be a fairly
advanced project, however, so I suggest you get plenty of building in before you
attempt it. I think it could be a very unique and fun project and should be a
very attractive model. Designed properly it may be an excellent flyer, but
again, building experience will be essential before you attempt it. Otherwise
it will be an exercise in misery and frustration – take it from someone who
jumped in way over his head too early.
Top
|
|
|
I ordered a set of Palmer plans for the 11-foot C-130 and if
you are not familiar with Palmer there is minimal information provided with the
plans and no advice/information offered after the purchase of the plans. I
have a couple of questions about the construction of this aircraft and must
search for answers. For instance, the main strength of the fuselage
lies in a section about 4 foot long, by 9 x 11 inch rectangle located directly
under the wings and cg. This is made of 1/4" x 1/2" medium hard balsa
sticks running lengthwise and crosswise making this rectangular box. Cross
bracing is provided by 1/4" sq. sticks at various places.
Then the roundness of the fuselage is created with balsa
formers at various fuselage stations, longerons, and planking. Well, my
question would be: Do you think this rectangular box would provide better
strength to the fuselage if those 1/4" x 1/2" sticks were of Basswood instead of
Balsa or would the change be so minute compared to the increase weight of the
basswood?
Palmer is only suggesting 49 MVVS engines on this airframe
so he suggests building it as light as possible. Then he turns around and
suggests the use of 1/8 inch foam board instead of light (contest grade) balsa.
I can only obtain 3/16 inch form board here, and yes it is cheaper then balsa,
but question if it is better and the practicality of foam board vs. balsa.
The foam board I have weighed is heavier then light balsa! Any thoughts on
your part would be appreciated.
You’re going to have to take my comments for what they’re
worth here. I’ve never built anything like the project you’re working on, so
I’ll go from general experience and you can adjust fire.
I would use medium density balsa for the longerons and not use
plywood anywhere that it isn’t absolutely necessary. For example, if the design
calls for lite-ply formers, I would replace them with balsa except in
strength-critical areas as I’ve already mentioned.
Many designers draw nice outlines and an adequate structure,
but also over-build their designs. I don’t have an engineering degree, but from
years of experience, I’ve learned that a lot of wood can be removed from a model
making it much lighter and still be airworthy. On this plane, I suggest you
skip the FoamCor and use balsa instead. It’s stronger and lighter as you have
said. It is more expensive, but my way of thinking is that if I can’t afford to
build it right, then I can’t afford to build it.
Think about where the forces are going to be in this plane –
the engine mounts, wing attachment, wing center section and landing gear. Most
of that load is carried by the skin or the spars. The lighter you build it, the
less load on all areas so building light has a snowball effect in a good way.
The box construction is there for a couple reasons: One, it
makes it much easier to install equipment in the fuselage than if the inside were
round. Second, and more importantly, it allows you to build a straight box
around which the rest of the fuselage is built. A round, planked fuselage is
amazingly strong and light. If it weren’t for building ease, the box would not
be necessary. If you were to build just the outer formers with planking and
reinforcement where necessary (wing mount, empennage, etc) your fuselage would
be adequately strong.
However, it is very difficult to build a round fuselage that
is straight – hence the box. This plane has 2.0 cubic inches of engine total,
so keep that in mind. Try not to think of it as a four engine airplane, but one
having a single 2.0. The fuselage as designed is probably over-built already.
1/4 x 1/2 balsa box is fairly substantial. Now it is a big box, so it has to be
built straight and the cross-braces should be as close to a perfect fit as
possible to prevent it from flexing. Once you get this monster planked, you
will not be able to twist this fuselage no matter how hard you try. If you
glass it, which is what I would do, it will be that much stronger.
For the most part, there is very little force on ribs. When
designs start getting larger, designers make ribs thicker to make the plane
easier to build. Thicker ribs are stiffer and easier to work with on the
board. But in the air, they do very little so that ease of building has a
price.
If you want to use 1/8” ribs, then cut a big chunk out of the
middle. You can remove at least half the weight of every rib. I wouldn’t mess
around with ribs in the nacelle area too much though. But it is only a .49.
Don’t make the mistake of thinking that each nacelle has to carry that 2.0. A
3/16” firewall is more than adequate for each engine. If the firewall is small
enough, you might even get away with 1/8”, but I’d have to see the design before
recommending that.
Another area where I often see planes being over built is the
thickness of the skin and sheeting. Often on larger planes the skins are too
thick. I believe they do this to give you lots of material to sand to get it
flat. However, if you do a good job sanding the ribs before sheeting and sand
the skins before gluing them on, then you can get away with thinner skins to
begin with.
I would think this plane would be strong enough with 1/16”
skins on the wing that are subsequently glassed. I’ve seen planes of this size
with 1/8” skins which is ridiculously thick. At most they should be 3/32” but I
believe you could use thinner skins with no compromise to the strength.
Whatever you use for skins, make sure they are the lightest wood you can find.
The bottom line is that (again, I haven’t seen this design) I
think you would do better to “unbeef” this design than to beef it up. No matter
what you do, if this thing crashes, it’s going to explode, so may as well make
it light so it flies well.
Top
|
|
|
What technique did you use when making
grooves in the wing spars for the
shear
webs? Was there some tool or procedure required to make straight,
uniformly deep grooves?
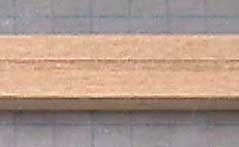
I used to use my
router
table, but now I use my
table saw.
Top
|
|
|
When gluing the
ribs and webs to the bottom
spar, how do you go about keeping them perpendicular to the spar? I
did not see any clamp or brace on each rib to ensure it dries straight.
I cut the webs so that they hold the ribs in the proper
position. For most ribs that means perpendicular, but for the center ribs
on a wing having
dihedral, I cut the proper angle on the shear web. Before the glue
sets up, I add the upper spar to ensure the shear webs are standing
perpendicular.
If I wait until they are dry before adding the upper spar,
then if the webs do not align properly, I will have to cut them loose. It is
better just to complete the job and get it right the first time.
Top
|
|
|
You said that you keep the ribs straight with the use of the
webs which are cut square. Two questions arise:
1. What if the plans do not call for webs?
I generally add webs to most planes I build. They are
light, add tremendous strength and also help prevent the wing from twisting
— especially
unsheeted wings.
2. Making the webs square helps align them perpendicular
left to right, but what about making them perpendicular when looking at the
plane from the side, i.e. leaning forwards or backwards?
I align ribs over the plan or over gridlines to ensure they
are straight fore to aft. As far as leaning forward or backward, any
decent kit or plan will tell you how to build the wing with the ribs on the
board. For flat bottom
airfoils, the wing is built flat on the board.
For symmetrical or semi-symmetrical wings one of two methods
is used most commonly. Either a stick is placed under the ribs at the
trailing edge so that the ribs align properly with the main spar flat on the
board or the ribs have tabs on the trailing edge that align them with the main
spar flat on the board. The tabs are removed after the wing is removed
from the board.
As far as ensuring the webs are perpendicular, I notch both
the top and bottom spar and make sure I can get both spars glued in place before
the glue on the webs sets up. The notches align the webs vertically.
Top
|
|
|
I built a 4*60 with CA glue mostly,
some epoxy and minimal wood glue. I have discovered that I may have some
allergic reaction to CA. I am a bit cautious now with CA and certainly
would like to migrate to using more Titebond. Here are a few questions
which I hope you could throw some light on (hope you do not mind me using the
4*60 manual as a reference, and I assume that you've built this popular model
before) :
1) Which is better, the
regular Titebond or the waterproof Titebond ? Do they have the same drying time
and strength ?
2) If you take a look at step 2d of your 4*60 manual, how would you
apply Titebond? With CA it is pretty easy, just dry assemble, and hit the
joints with CA. Now with Titebond, it seems like you would have to apply
beads of glue along the edges of every rib,
shear web, diagonal braces, etc
before you assemble EACH piece. How do you clamp the assembly ?
3) For applying balsa sheeting onto the stabs (step 42b), do you use
Titebond? Does warpage become an issue here ?
First, I have not built the 4 * 60 kit that you
are referring to. However I am familiar with the aircraft. It is a
typical sport R/C model using typical construction methods as far as I can
tell. A lot of people have reactions to
CA and have either switched to
"odorless CA" or a different type adhesive. I do not have a reaction to
CA but I do not use it for general construction because it is messy, expensive
and does not have a long enough working time. I have also found that it
does not speed up my construction.
I have used Titebond for many years and have
never had any type of problem with it. I recently tried Titebond II but
found that it seemed to dry a little more rubbery and tended to clog
sandpaper. When that bottle was gone I switched back to regular
Titebond.
This
How-To
shows how I build a typical wing using slow drying Carpenter's glues.
Top
|
|
|
In your latest section about creating the ribs, you show how you cut
out a portion of the middle of the ribs. I was wondering if that takes
away from the strength of the ribs or if the real pressure is not on those areas.
This question
was in reference to the article
Create a Set
of Constant Chord Ribs. A section has been added to that page to
address this question specifically.
Top
|
|
|
I am looking into scratch building a Embraer 135 RJ, because I have
some friends who fly them and I just want to fly R/C airliners. I have not decided
on what power plant I am going to use......(i.e. gas or electric DF). I
was hoping to use gas because of the size and scale like performance. I am
not sure what the materials should be... foam or fiberglass considering
strength, since the wings do not have a huge wing area. What about actually
sculpting the airframe? Is the process a hard thing to do? What
about getting a hot wire system? Are they worth the money?
In a subsequent e-mail this builder indicated the fuselage
diameter to be approximately 8".
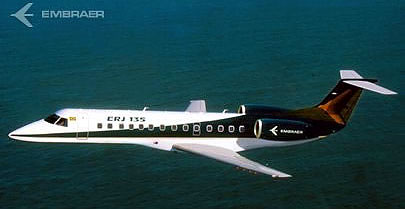
Keep in mind that I have never done this, but
this would be my approach for ease of building and accurate outlines as well
as light weight. I looked up this airliner on the web so I could see what it
looks like.
If the plane was smaller then I would say cut
the whole thing from foam and then fiberglass it. But with a fuselage that
large around I would build a box made of balsa. Around the box I would
strategically place formers. Between the formers on the outside of the box I
would glue blocks of foam and then carve it to shape. You could build the
whole fuselage from foam but you would have to glue blocks of foam together
first and then cut fuselage sections.
The last option is to build the fuselage from
balsa and plank it. That’s what I would do if it were a really large
airplane, but probably not for the size you’re building.
I think you should definitely make the wing
from a foam core and sheet it. No matter how you build the model, I
would definitely
fiberglass it.
As far as buying the foam cutting equipment,
you’d probably have to for a project like this unless you know someone who has
it and is willing to loan it to you or help you out. If you build more
airliners then you’ll become an expert with the tools and each model should be
better than the last.
If this is your first model, then try to look
at it as a learning experience and don’t be discouraged if the end product
isn’t quite what you envisioned.
Top
|
|
|
|
|
|
Back to Mail and FAQ
Airfield Models Home |
|
|
Copyright © 2002-2007 Paul K.
Johnson |
|
|