Lightening Wing Ribs
I
received an e-mail from a person who wanted more information about the
strength of a rib that had large internal sections removed. It is a
legitimate concern simply because nobody wants to build a model that
self-destructs in flight.
I have used ribs similar to this in several of my
models and have had no problems. To date not a single rib has broken
in flight or from handling. However, you do have to be careful when
handling the wing. For example the ribs used for
Great Gonzo have a 1/4" outline. The
wing must be lifted by grasping the spars or the
center section sheeting.
There is a good possibility that the rib would break if the wing were lifted
by supporting it under a rib.
I have had to repair
Great Gonzo three times due to damage that occurred on the ground on
exceptionally windy days. The first damage was caused when Great Gonzo
blew off a table at the field and fell several feet to the ground. It
flipped over in the air and landed upside-down directly on the wing which flexed and
tossed the model back into the air. Damage incurred was a broken
leading edge near the
wing root.
The other two times both occurred during
take-off. Great Gonzo was blown over when it turned cross-wind (pilot
error) and cart-wheeled several times. The first time this happened a
main spar was broken as well as the leading edge. The second time the
tail end of the fuselage had a minor crack and the leading edge of the wing
broke again. Notably, no wing ribs were broken in any of these
incidents.
My Stik 30 has
smaller cut-outs because the model was designed for higher performance.
As I mentioned on the My Stik 30 page, the ailerons can deflect up to 45° in
each direction on high rates. The roll rate is so fast I can not count
them. Additionally, when the Webra .32 was mounted on it I put the
model in several full-throttle, terminal-velocity dives of several hundred
feet. The airframe had no problems with this.
My Stik 30 uses the same wing that was on the
first version that I crashed on take-off at full throttle. That crash
was due to putting a wing tip in the ground and cart-wheeling the plane (my
favorite way to break airplanes apparently) across the field.
The wing
was subjected to a significant torsion load but the only damage to it were a
couple dents in the wing tips and a broken turbulator spar. None of
the ribs were damaged. The fuselage was totaled.
As far as weight savings goes, it is all
relative. If you are trying to shave every ounce of weight from your
aircraft,
then the effort to remove weight from the ribs is worth it. On the
other hand, the weight savings of the ribs alone probably is only an ounce
or so for a .40 size ship assuming the use of contest balsa. If the
ribs are made from heavier wood then the weight-savings will be greater.
The following images show the wing construction
of My Stik 30. Again, this wing survived a full throttle cartwheel
across the field and is still in use.
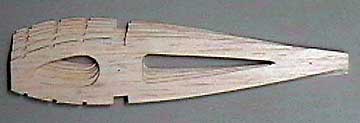 |
My Stik 30's wing has turbulators on the top
and bottom of the forward portion of the wing and cap strips on the aft
portion of the wing. |
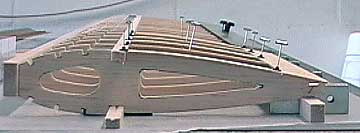 |
Note the shallow
grooves in the spars (a little deeper than 1/64"). These make it
very easy to align the shear webs between the spars and provide
additional gluing area. The grooves can be cut on a
table saw or
router table.
The black items you see on the T-pins are
called Pin Clamps and are manufactured by Rocket City. |
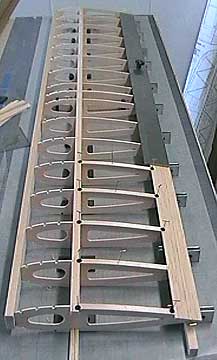 |
Another view of the wing
under construction. The wing is light and strong. There are
twelve one-piece, full-span wood strips in the construction:
-
3/8" x 3/4" Leading edge (1)
1/8" square Turbulators (6)
1/4" x 3/8" Main Spars (2)
1/16" x 1-1/2" Trailing edge sheet (2)
3/8" square Trailing edge (1)
|
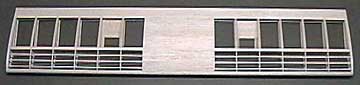 |
The completed wing. |
|