Metal Working Tools
If you are a scratch builder then you will undoubtedly have to do some
metal
work. For sport models, metal work is usually limited to fabricating
landing gear, soldering various fittings and bending
brass fuel lines. For
scale aircraft models, any number of fittings may need to be fabricated in
your shop.
A bench vise is sufficient for bending dural aluminum gear. If
it does not have smooth jaws you can pad the jaws with scrap hardwood or
aluminum. If you are bending
music wire gear then the bench vise is not a good idea.
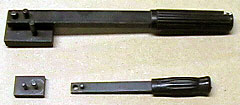 |
Music wire is tempered and will crack if the bend radius is
too sharp. For that reason I recommend using a dedicated wire bender.
I use the K & S Mighty and Mini wire benders and have had good
success with both of them. Wire benders have two steel dowel pins
—
one holds the wire in place and the wire is bent around the second.
The K & S models come with a bending lever. |
I use a moto-tool with an
emery cut-off wheel to cut music wire. Do not attempt to use side
cutters to cut music wire. The wire is too hard and will ruin the cutters.
A scroll saw with a fine metal cutting blade and
plenty of oil will cut aluminum plate. I normally draw the cut
lines on the aluminum with a Sharpie fine point marker and then put a piece of
clear packing tape over the line. The packing tape becomes a lubricant and
protects the line.
My soldering iron is a 25-watt model that has performed very well.
It is nothing fancy. I think I paid about $15 for it many years ago and
it is never given me any problems. A heavier duty iron with a bigger tip
is better when soldering larger areas such as wire wrapped landing gears.
The problem most people run into with
their soldering irons is that they do not tin the tip properly. You
need a wet sponge to wipe the tip on while you are soldering.
Melt some solder on the iron tip after the iron is hot to put a shiny plating
on it. If the tip will not take the solder then it is not clean.
Wipe tip on the wet sponge and try again. Repeat until the tip will take
the solder. For particularly stubborn tips I dip the hot iron in a tin of
paste flux and let it sizzle for a few seconds.
A small butane torch is good for times when the joint to be soldered
is too big for an iron. The trick to soldering is to two-fold:
-
The metal being soldered must be cleaned. Use
fine steel wool or
very fine wet or dry sandpaper to remove tarnish and give the metal a little
"tooth."
-
Heat the work, not the solder.
The solder will flow beautifully when the metal is hot enough. Do not
heat the work any longer than necessary. Get it heated quickly, apply some flux,
apply the solder and then let it cool.
Allow soldered joints to cool naturally. Do not cool solder joints by dipping
them in
water.
A solder joint that is cooled too quickly will crack.
|