Drilling the Engine Mount
There is not much tolerance for error when drilling an
engine mount. I strongly recommend that you use a drill press and seek
assistance if you have never done this before. If the holes are off enough
to make it difficult to thread in the bolts then the mount or crankcase may
crack or the bolts may break under additional stress. Obviously these are
bad things that you don't want to happen.
I use a blind nut (AKA T-nut) that fits in the mounting
hole on the engine lug. You can get blind nuts in sizes from 2-56 up.
Remove the barbs from the blind nut or bend them down so they are flush with the
flange. Remove the head from a screw and then
chuck it into your drill. Use a file to put a point on the end of it.
Four sets of these allow you to mark all the mounting holes.
It helps if
you find a way to clamp the engine to the mount while marking the holes.
Place a punch over the headless bolt and tap it with a
small hammer to mark the mount. If you can clamp the engine to the mount
then tightening the clamp will usually mark the hole locations well enough that
you will not have to use the hammer. Save
these sets as you make them for use next time.
Marking
Bolt Locations on an Engine Mount
|
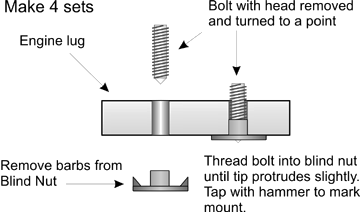 |
You can use the engine measurements included with
the engine to drill the mount, but you have
to be able to measure accurately. If you are using a nylon mount, the
engine may spread the arms of the mount when you put it in. Obviously the
holes will not be spaced as they were when you drilled them.
My suggestion is do not
use a mount that is a squeeze fit on the engine. You can usually file away a
little of the upper inside corner of each arm so the engine does not
rub against the arms. The only part of the engine that should touch the
engine mount is the bottom of the mounting lugs.
If you are using a plastic mount do not
lubricate the bit. Use a slow speed on your drill or drill press
so that you do not melt the plastic. If you are drilling a metal mount,
then use some type of oil to prevent galling, over-heating or premature dulling
of the bit. I just use whatever oil is handy — usually sewing machine oil.
If you decide to tap the mount (which I recommend),
then be sure to back the tap out frequently to clear chips from the cutting
threads. If you fail to do this you may break the tap. At that point
you may as well buy a new tap and engine mount unless the tap broke far enough
from the mount that you can grip it with pliers and back it out. You might
save the mount, but you will still need a new tap. Some engine mounts and all beam mounts have beams
that are parallel (top and bottom of beam) so that a bolt and locknut can be used to hold the engine in
place. Many engine mounts have beams that are not parallel and are
designed to be tapped for the engine bolts or use sheet metal screws.
Personally, I prefer to tap all mounts because I have seen too many people have
problems with nuts vibrating loose, mounts crushing, etc. If you install
your hardware correctly, you shouldn't have any of these problems, but if you
tap the mount, then these problems are not an issue.
Tip: If you tap a
plastic mount, measure the amount of bolt that will thread into the mount.
After drilling the holes, tap all but the last 1/4" that the bolt will thread
into. This will turn the mount into a self-contained lock-nut.
Nylon-insert lock nuts are designed for one time
use. If you remove the nut you should replace it because the nylon will not
work properly afterward. Also, if the engine gets hot enough, it can also
heat the bolts to the point where the nylon insert softens. Obviously this will
destroy it is "locking" properties.
A lock nut can realistically be removed a couple of times and still be ok,
but if it gets to the point where it threads on with little force then it is not
a lock nut any more.
|