Pushrods
Short Pushrods
Short rods are typically made from a piece of threaded rod. One
end can have a bend (see next section) or a solder clevis. The
threaded
end usually has a threaded clevis or a ball link.
1/16" music wire can also be used. Again, one end can employ a
bend and the other end can have a solder coupler and threaded clevis.
At times, it is possible to put a bend in both ends making the pushrod
non-adjustable.
Long Pushrods
Longer pushrods can be solid wood, such as a balsa or spruce stick or a
birch dowel. While each of these are adequately strong if the
correct size is selected, they have a problem that is inherent in wood
— shrinking and expanding due to climatic conditions. This
will change the trim of the aircraft from one day to the next. I
avoid wood pushrods.
To make a wood pushrod, drill a hole in the side that is the same size
as the threaded rod. Drill the hole about 2" from the end of the
pushrod. Put an L-Bend in the threaded rod and insert it in the
hole. Wrap heavy thread around the pushrod and threaded rod to
secure it in place. Finally, coat the threaded areas with glue.
A more stable pushrod can be made from a fiberglass or carbon fiber
tube. A small hole is drilled about 1-1/2" to 2" from each end of
the tube. A threaded rod with an L-Bend on one end is put in the
tube with the bent portion engaging the hole.
The end is then
plugged with a dowel that has a groove to slide over the rod. The
dowel is glued in place with CA or epoxy. Be sure the dowel does not
have to be forced into the end or the pushrod may crack. The dowel
should be a slip fit. It is a good idea to wrap
some thread or glass cloth around the ends of fiberglass or carbon fiber
pushrods to prevent them from splitting.
The other ends of the pushrod has a wire having a bend, clevis or ball link
attached. This type of pushrod is very rigid and stable and
generally does not need any type of support to prevent flexing unless the
tube is very long.
Very Long Pushrods
In same cases you may have a pushrod that is so long that it will flex
— even if made from fiberglass or carbon fiber tube. If this is the
case, then you are probably building a large airplane and should look at a
different system, such as Pull-Pull or servos mounted near the control
surface. The end result will be stronger and lighter.
If you must use a long pushrod, then it needs to be supported at
intervals along its run to ensure that it can not flex.
Tube-In-Tube Pushrods
Tube-in-Tube pushrods are very popular as well. These are
flexible and must be anchored every 3"-4" to ensure they are rigid.
Do not use pneumatic tubes that are sold by some companies as tube-in-tube
pushrods. They have too much drag and will cause all types of trim
problems. Instead use a system specifically designed for model
aircraft such as Sullivan NyRods.
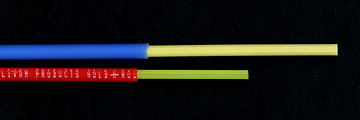 |
Two styles of Sullivan NyRods. The blue NyRod is
larger in diameter and stronger than the red version. The outer casing
must be anchored every few inches to ensure the pushrod is rigid.
Note the splines on the yellow inner. These splines reduce friction
and allow smooth movement. |
Besides anchoring these pushrods, you should also ensure that the inner
portion is adequately stiff from where it exits the fuselage to where it
connects to the control surface. Often there is five or more inches
of unsupported pushrod. The fix to this is to only allow about 2" of
the inner pushrod to exit the fuselage. The rest of the run should
be a threaded rod.
Alternatively, you can slide the same length of threaded rod into the
inner pushrod until the threads engage. Turn the threaded rod into
the pushrod several turns and it will be secure. You can also use a
file to notch the unthreaded portion of a threaded rod and use CA to glue
the threaded rod into the pushrod. |